- 1. Process flow chart
A. Preparation Work
B. Electrofusion connection
C. Appearance inspection
D. Next process construction
2. Preparation before construction
1). Preparation of construction drawings:
Construction in accordance with the design drawings to carry out. When the design unit has an effective construction drawing, the construction unit should go to the construction site to understand the specific situation. For the part that cannot be constructed according to the drawing, it should disclose and negotiate with the design unit to determine whether special construction technology or local design changes can be adopted. At the same time, materials and equipment should be purchased according to the drawings, and the construction schedule should be arranged.
2). Personnel training:
Operators engaged in polyethylene gas pipeline connection must receive special training before taking up the post, and can only take up the post after passing the examination and technical assessment.
In addition to the theoretical knowledge of gas knowledge, characteristics of polyethylene special materials, electrical knowledge, polyethylene welding equipment, polyethylene gas pipeline construction technology and other aspects of the training personnel, and participate in the assessment.
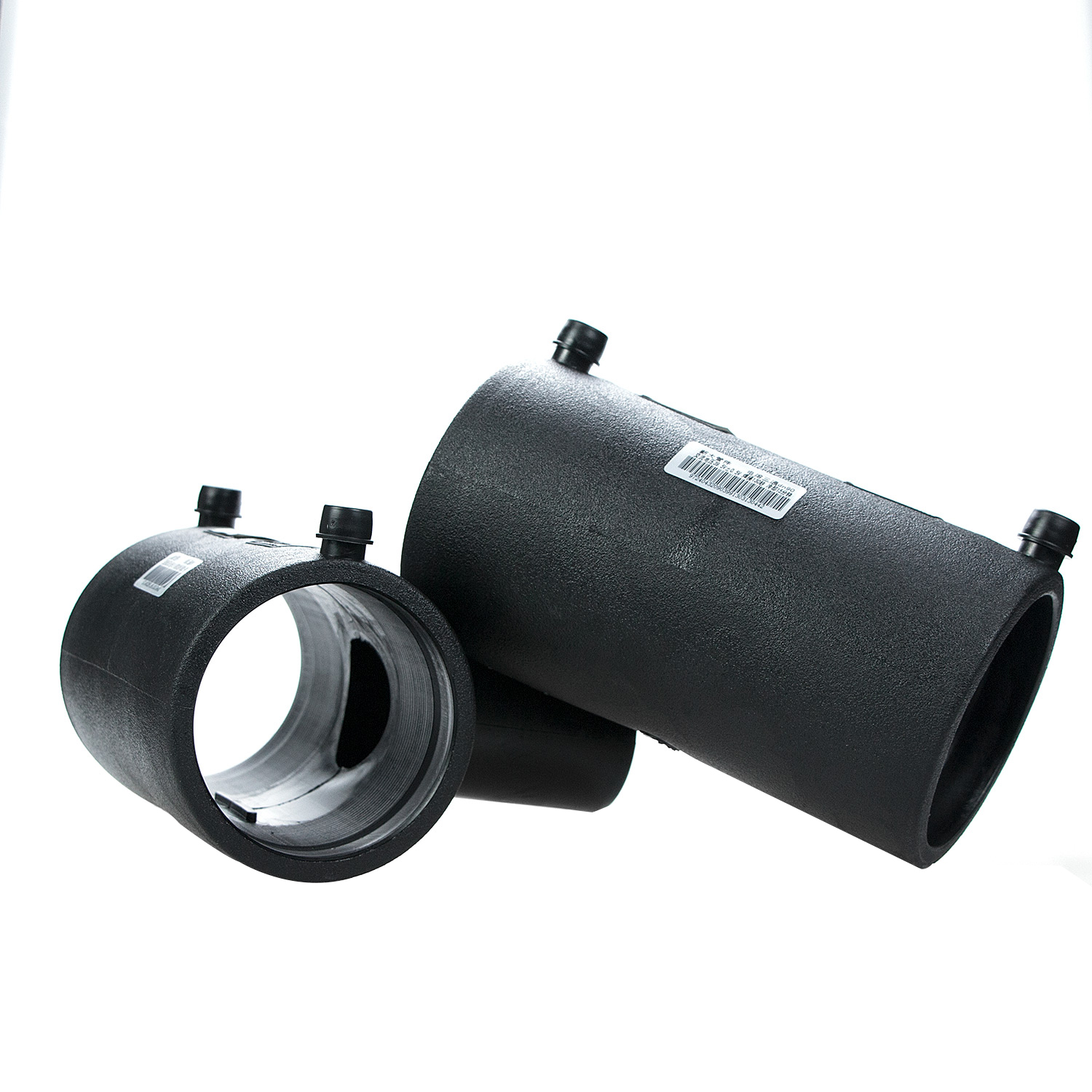
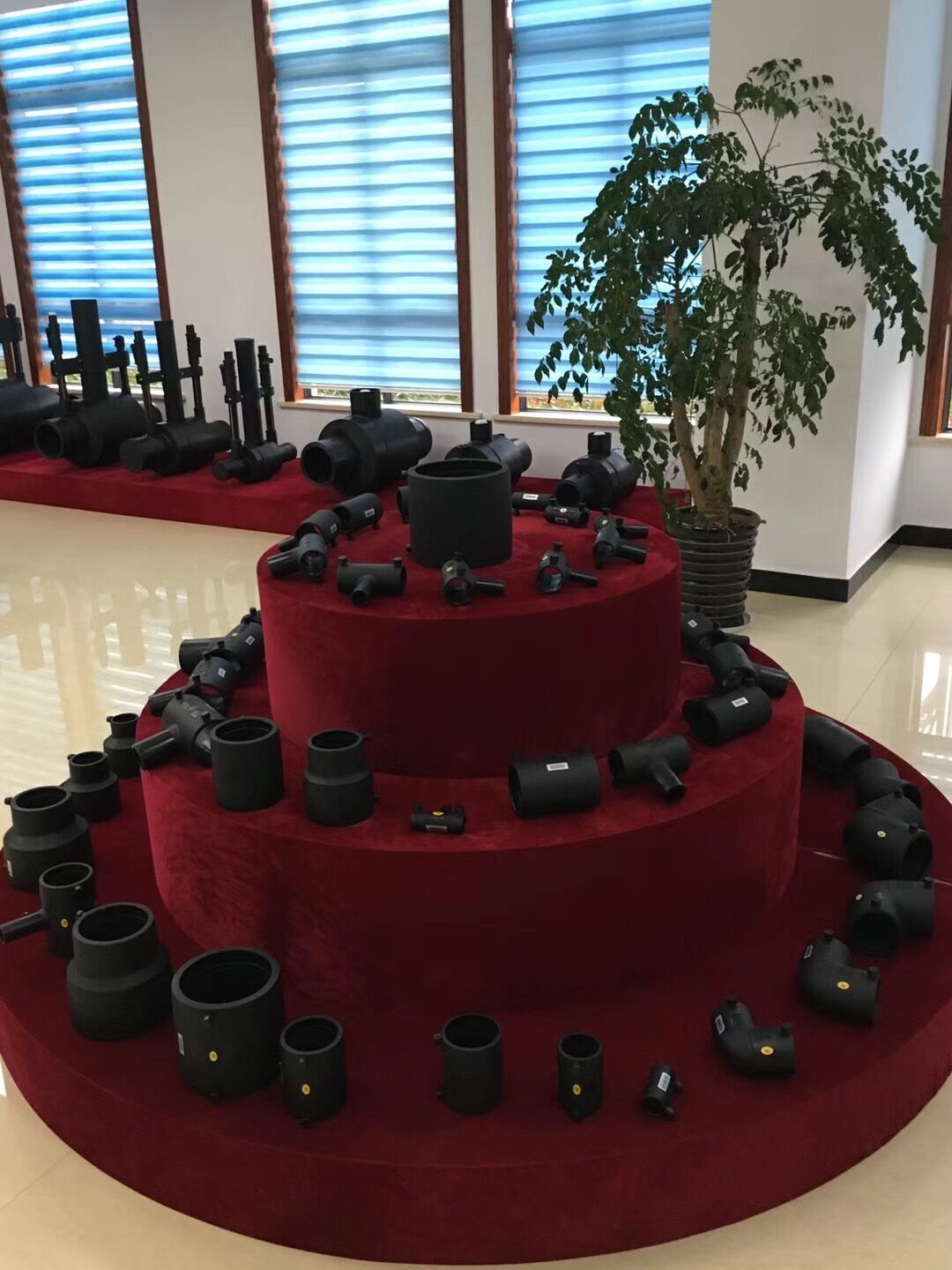
3 ).Preparation of construction machines and tools
According to the requirements of construction technology, prepare the corresponding construction machines and tools. Because there is no unified standard for the welding quality and welding parameters of polyethylene pipes in our country, the welding parameters of pipe, pipe fittings and PE ball valve produced by different manufacturers are different. In order to achieve reliable welding effect, in the selection of equipment must also be carefully selected, choose good quality products, in the welding effect, to be reliable.
a) Automatic electrofusion welding machine
b) 30Kw diesel generator
c) Fix the fixture
d) Rotate the scraper
e) Plate scraper
f) Clamping tool
g) Rotate the cutter
h) Flat ruler
i) Markers
3. Acceptance of pipe, fittings and PE ball valve
1) Check whether the products have factory certificate and factory inspection report.
2)Check the appearance. Check whether the inner and outer surfaces of the pipe are clean and smooth, and whether there are grooves, drawings, dents, impurities and uneven colors.
3)Length check. The length of the tube should be uniform and the error should not exceed plus or minus 20 mm. Check whether the end face of the pipe is perpendicular to the axis of the pipe one by one, and whether there are pores. Pipes of different lengths shall not be accepted before the cause is identified.
4)Polyethylene pipe for gas use shall be yellow and black, when it is black, the pipe mouth must have an eye-catching yellow color bar, at the same time, there should be continuous permanent marks with a distance of no more than 2m, indicating the purpose, raw material grade, standard size ratio, specification size, standard code and serial number, manufacturer's name or trademark, production date.
5)roundness check: The arithmetic average of the test results of the three samples is taken as the roundness of the pipe, and its value greater than 5% is deemed unqualified.
6) Check the diameter of pipe and the thickness of bi. The diameter of the pipe shall be checked with a circular ruler, and the diameters at both ends shall be measured. Any unqualified place shall be deemed as unqualified.
The inspection of the thickness of the wall is carried out with a micrometer, measuring the circumference of the upper and lower four points, any one is unqualified.
7) Pipe, pipe fittings, PE ball valve transportation and storage
Transportation and storage of polyethylene products shall be carried out in the following ways: Nonmetallic rope should be used for binding and hoisting.
8)Shall not throw and by violent impact, may not drag.
Shall not be exposed to the sun, rain, and oil, acid, alkali, salt, active agent and other chemical substances contact.
9) Pipe, fittings, PE ball valve should be stored in well-ventilated, temperature is not more than 40℃, not less than -5℃ in the warehouse, temporary stacking in the construction site, should be covered.
10 ) In the process of transportation and storage, the small tube can be inserted into the large tube.
11 ) transportation and storage should be placed horizontally in the flat ground and garage, when it is not normal, should be set up flat supports, the spacing of the supports to 1-1.5m is appropriate, pipe stacking height should not exceed 1.5m.
12) It is suggested that the storage period between production and use should not exceed 2 years, and the principle of "first in, first out" should be adhered to when distributing materials.
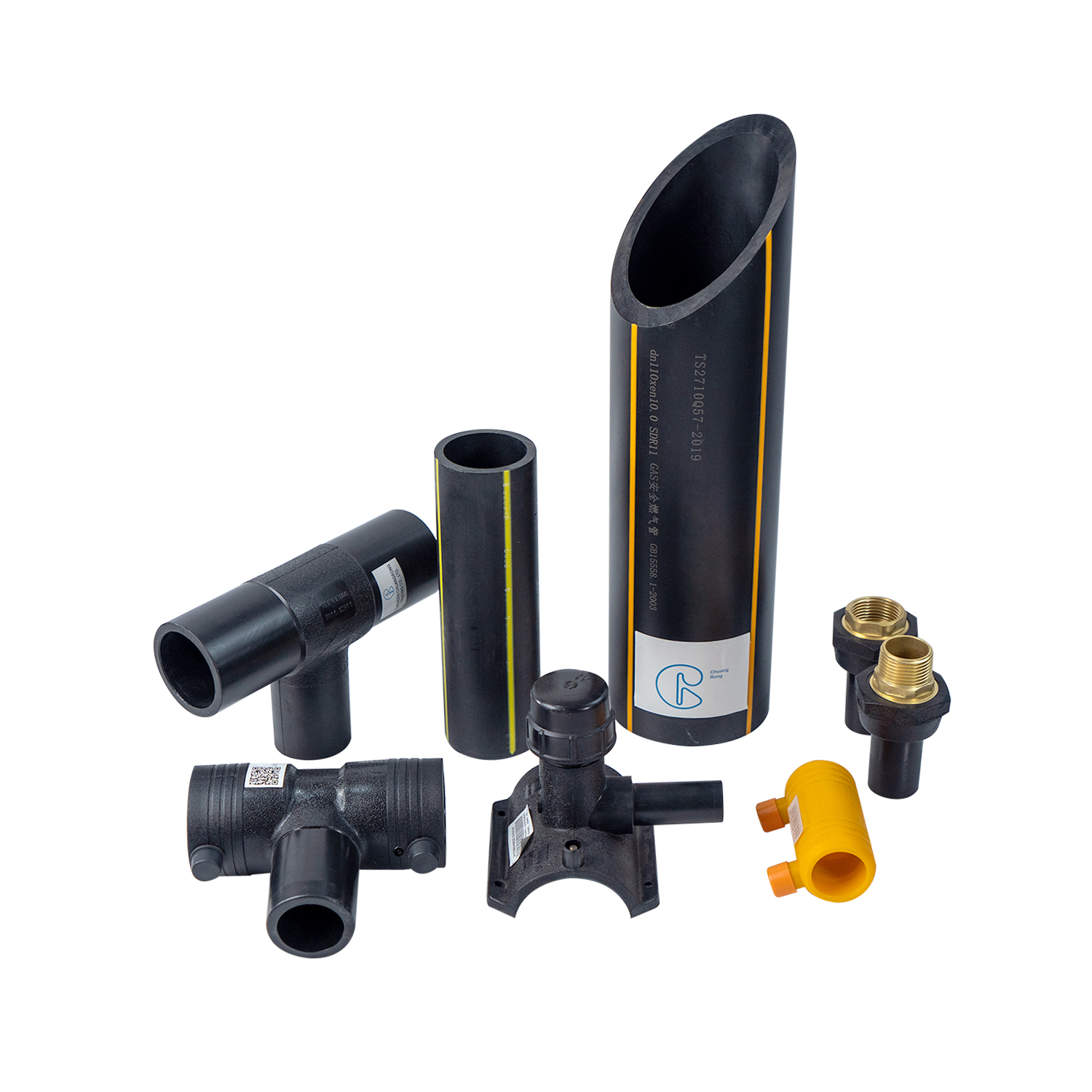
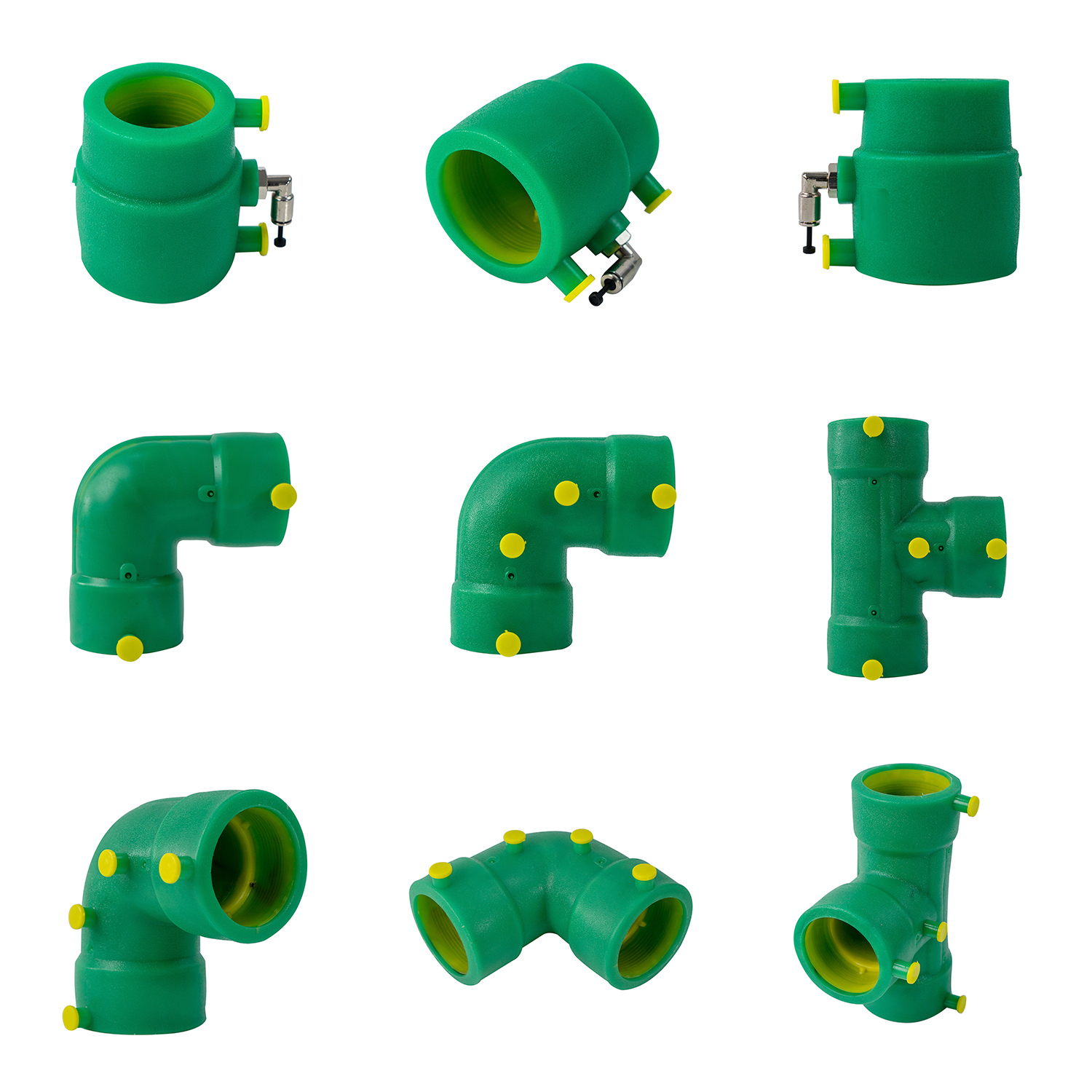
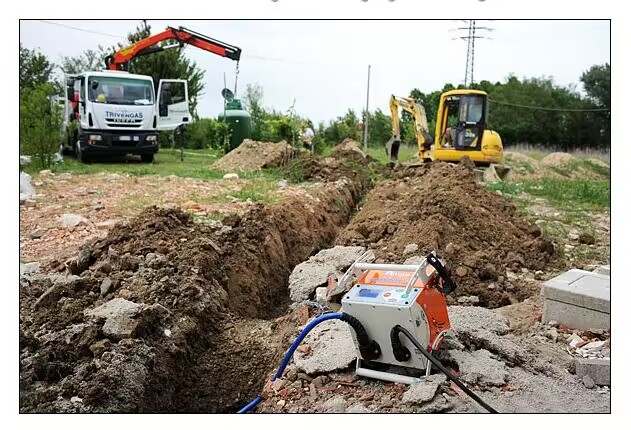
![V17B]@7XQ[IYGS3]U8SM$$R](http://www.cdchuangrong.com/uploads/V17B@7XQIYGS3U8SMR1.jpg)
4 Connection steps of electrofusion welding
1). Connect the power supply of each part of the welder. Must use 220V, 50Hz AC, voltage change within ± 10%, power supply should be grounded wire; Prepare auxiliary tools such as marker, flat scraper, flat ruler, and fixing fixture.
2) Prepare the pipes and fittings to be welded, and do not open the packaging of the weld fittings too early.
3)Three installation: remove the outer package of pipe fittings, the registered pipe fittings into the pipe fittings to be welded to do the marking place installation; Install the fixing fixture and fix the assembly to be welded with furniture; Open the electrode jacket of the pipe fitting and install the output electrode of the electric fusion welder on the pipe fitting electrode.
4) Operate the welding machine according to the operating procedure to the position of input welding parameters, manually (parameters provided by the pipe fitting label)
5) Start the electric fusion welding machine to start the welding process, and the machine will automatically detect the ambient temperature and adjust the welding parameters. After the welding process is completed, the machine will automatically stop the welding and cooling time. After the cooling is completed, the electrode and fixed fixture can be removed for the next section to be welded.
6) Print the welding process parameter record or later centralized printing.
5. Welding process parameters
Operate the welding machine according to the procedure. The parameters are provided by the pipe fitting label.
6. Quality check of electrofusion pair interface
1) Weld appearance quality inspection : Inspection method: visual inspection; A ruler is measured.
2 )Check items: concentricity; Observe the material overflow of the hole.
3) Qualification criteria: fault opening is less than 10% of pipe wall thickness; The fusion pipe fitting is tightly combined with the pipe and uniform; Welding process without smoking (overheating), premature shutdown phenomenon; The observation hole of the fuse fitting is protruded from the material. Meet the above conditions can be judged as qualified.
7. Safety measures
1) Operators should be safe dress: wear protective gloves; Wear work shoes; Wear protective glasses; (when grinding the workpiece) : with protective earcups, welding caps.
2 ) Equipment firmly grounded, leakage protection switch.
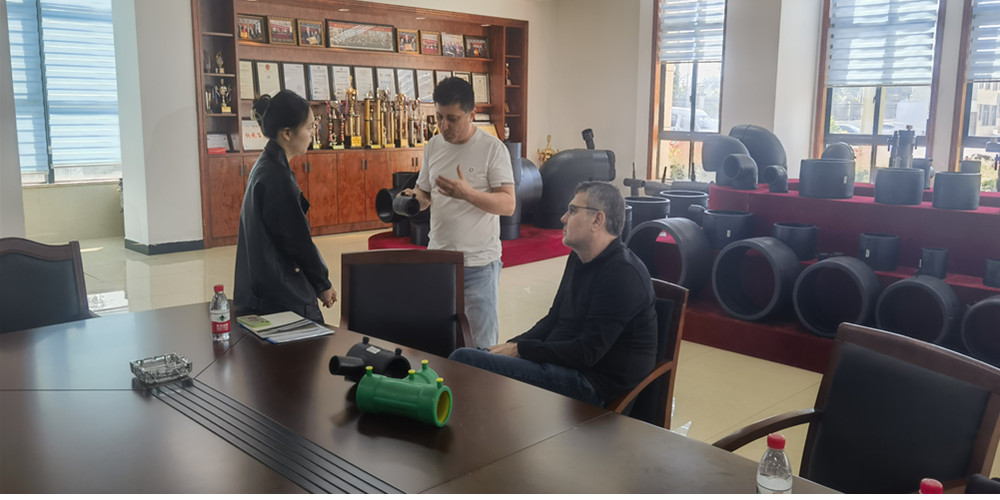
CHUANGRONG is a share industry and trade integrated company, established in 2005 which focused on the production of HDPE Pipes, Fittings & Valves, PPR Pipes, Fittings & Valves, PP compression fittings & Valves, and sale of Plastic Pipe Welding machines, Pipe Tools, Pipe Repair Clamp and so on. If you need more details, please contact us +86-28-84319855, chuangrong@cdchuangrong.com, www.cdchuangrong.com
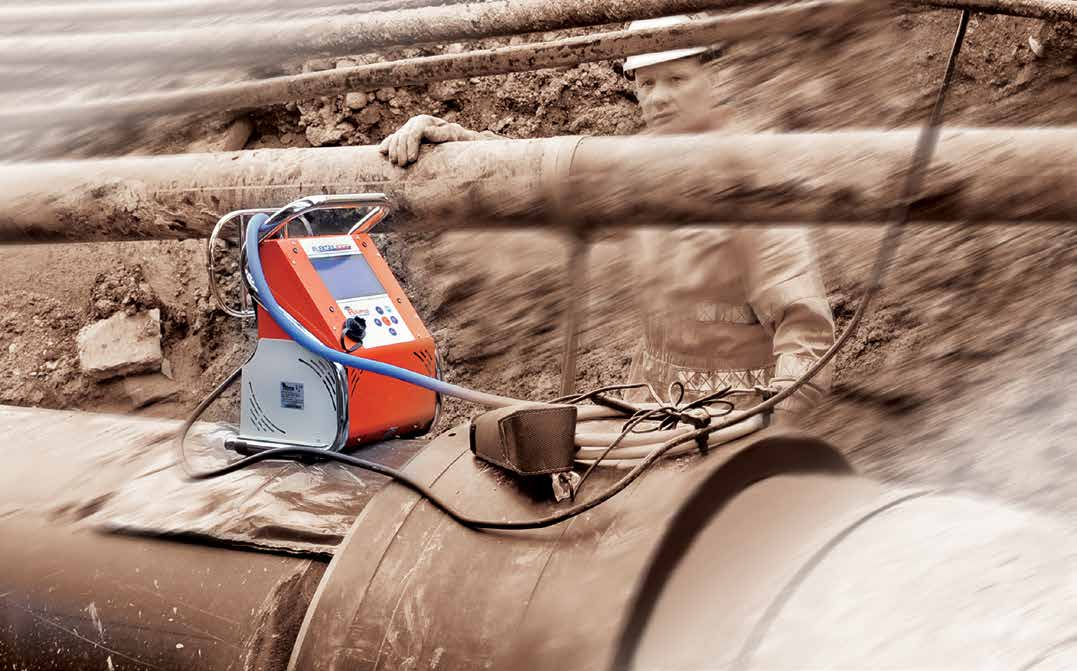
Post time: Nov-09-2022